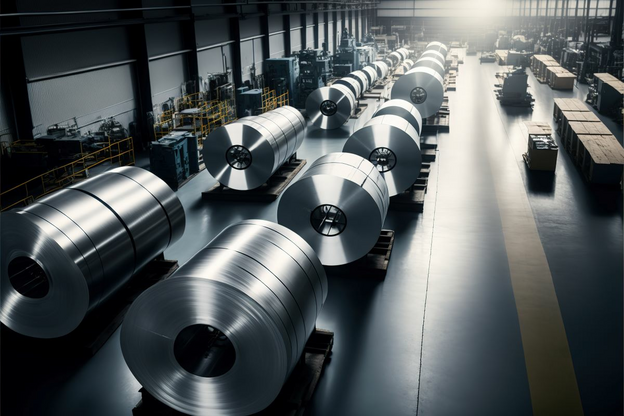
The metal industry is responsible for making all things functional and beautiful. They’re needed to create cars, buildings, equipment, appliances, fences, artworks, and many others.
As such, metal fabrication is an essential process in the manufacturing sector, often seen in processes like structural design and along the assembly lines. Global sheet metal fabrication service alone was estimated at USD$15.3 billion in 2022 and is projected to reach USD$17. 2 billion by 2026.
Metal fabrication encompasses various activities to make a finished product or component from sheet metals. It is typically done in machine shops, and metal workers include blacksmiths and iron workers. This article focuses on metal fabrication in the former environment.
Ready to understand how metal fabrication works? Let’s start.
Primary Processes Involved In Metal Fabrication
As mentioned, several processes are involved in metal fabrication. You’ll learn more about each of them as we go along. In the meantime, let’s take a look at the entire process.
- Preparation Stage
At this stage, the design and the product to be created or assembled determine the material requirements, shape, specifications, and succeeding fabrication activities.
- Measuring The Metal Sheet
The fabrication usually starts with a metal sheet with varying sizes and thicknesses, typically a quarter of an inch thick. This preferred thickness enables the metal to conform to various shapes. Metal fabricators use cutting, folding, and stamping techniques to make the desired shape.
However, other industries require thicker base metal plates. In such cases, fabricators use a gauge. But what is a sheet metal gauge? It’s a vital tool used in measuring the thickness of a metal sheet. They come in two primary classifications: a calliper gauge and an ultrasonic gauge. Choosing the correct metal plate gauge will depend on the type of metal you’re using and your project.
- Designing The Metal Sheet
Preparing the metal takes more than measuring and pinpointing the material you need. It likewise requires the metal to be designed accordingly. Most machine shops use computer-aided designs (CAD) that run computer numerical control (CNC) technology.
These technologies connect the design and fabrication machines, increasing fabrication accuracy and production levels. They benefit industries that mass-produce items without sacrificing quality and safety, like the construction, aeronautics, and auto manufacturing sectors.
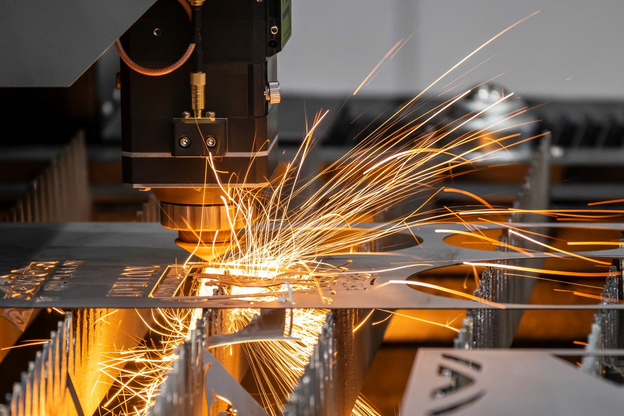
- Fabrication Stage
Metal fabricators are skilled professionals trained to perform challenging metal manipulation activities precisely. They may use one or more metal manipulation techniques to achieve their project. Below, you’ll find most of the activities used in metal fabrication.
- Casting: Involves pouring molten metal into a mould to get the desired shape of the metal to work on
- Cutting: One of the primary activities in metal fabrication, it requires fabricators to use different techniques, including laser cutting, sawing, and waterjet cutting.
- Drawing: This doesn’t include illustrating but instead uses tensile force to pull melted metal into a die. A die is a mould or pre-shaped tool used alongside a press to form a metal into its desired shape and size.
- Drilling: A fabricator uses a circular bit to drill holes into the metal plate.
- Extrusion: This method is used to make various products, including pipes, and is achieved by forcing billets through a die.
- Folding: A worker applies enough pressure onto a metal sheet to fold according to the desired angle.
- Forging: Requires a fabricator to use specialised machinery to compress a metal and shape or bend it accurately.
- Machining: Using multiple pieces of equipment, including drill presses, milling machines, and lathes, to fabricate metals into various forms and sizes.
- Milling: Involves drilling non-circular holes into the metal plate
- Punching: Lets metal workers punch pre-designed patterns into the sheet
- Shearing: Often done in the final stages, this activity removes unwanted material from the metal sheet.
- Stamping: This process forms a flat metal plate into specific shapes and often involves multiple activities like bending, piercing, and punching.
- Turning: Metal fabricators use this to cut metal by placing it onto a spinning machine.
- Welding: One of the most basic fabrication processes, welding occurs when a metal worker uses high heat to melt metal and other materials to join them.
Fabricators use different machines and techniques when creating a product or component, as can be gleaned from the discussion above. The ideal processes involved in such procedures will depend on the raw material’s shape and the end products’ requirements and purpose.
After completing one or a few of the processes above, fabricators will partially or fully assemble the end product.
Concluding Thoughts
Metal fabrication is an essential process that benefits multiple industries. It involves assembling partial or complete products and is thus a value-adding process that makes metals more functional and aesthetically pleasing. The sector’s products are a staple in our everyday lives, particularly inside and outside our homes.
To make a wide selection of products, fabricators must use varying technologies, methods, and pieces of machinery to fit a business’s specific requirements, as discussed in this article.